The Making of a Perrin & Rowe Tap
At Perrin & Rowe, we believe in small batch production to deliver unrivalled quality. All of our products are made to order in Britain so, although there will be a wait, you can be sure that your product has been built to last.
Perrin & Rowe’s reputation is built on British design and engineering. We have over 200 employees in the United Kingdom; from casters and machinists, polishers and platers and a dedicated customer service team.
The making of a Perrin & Rowe tap starts with a mould. For most of our brassware collections, this mould will be prepared in our foundry in the Black Country.
The brass we use is of the highest quality. Each ingot weighs 7 to 8 kilograms and is melted in a furnace at over 1700 °F. It takes skill, experience, and a measure of courage to ladle the molten brass into the cast iron dye.
As it cools, it is tapped out to reveal the casting. The casting must fully cool down before the excess brass can be cut away by hand, and all excess brass is returned to the furnace for use.
Each product is made up of several components, and our soldering team will attach finished parts from our machine shop to the casting. Perrin & Rowe combines traditional craftsmanship with cutting edge technology, and we use the latest CNC tools to precisely machine these components.
Polishing may sound simple, but it requires exceptional skill. Our team of polishers have a minimum of 10 years’ experience and have learnt how to achieve the best finish on hundreds of different products. We truly believe they are world class at what they do.
Every product is then quality-checked before going through the plating process. Our plating lines produce our stunning Chrome, Nickel, Pewter, Gold and English Bronze finishes, and each product is plated to a thickness that exceeds industry standards, ensuring a lustrous protective coating that is resistant to wear. Our three brass finishes (Aged Brass, Polished Brass and Satin Brass) are unlacquered, and leave the beauty of the natural material exposed.
After a final Quality Control check, the product is packed for final assembly. At the Perrin & Rowe warehouse in Rainham, our assembly team put all the components for each product together. Every single tap is pressure-tested with water before it receives a final polish and is boxed for despatch.
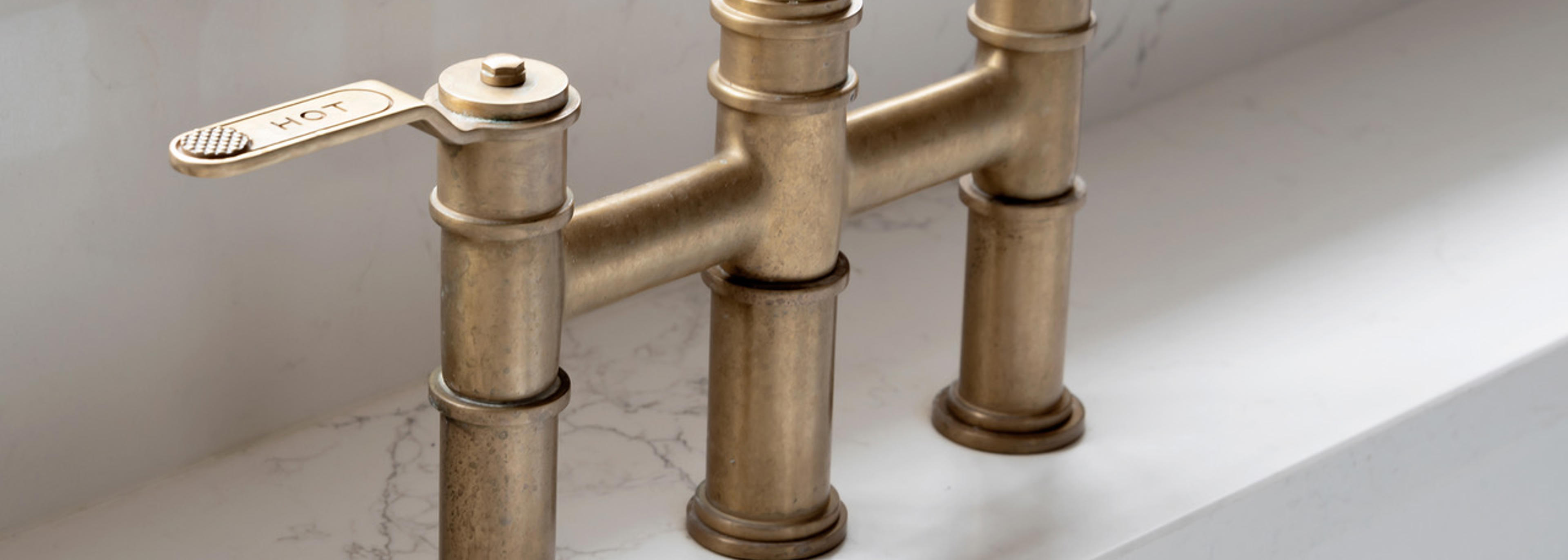
Caring for your Perrin & Rowe tap
We understand you want to keep your Perrin & Rowe product looking its best, so that it can be used and admired for years to come. We have a useful care and cleaning guide available to download as well as information on how to care for and treat our unlacquered brass finishes.
Inspired by the way you live
@annabarnettcooks
@halfpenny_at_home
@phoebenicol.interiors
@howarkdesign